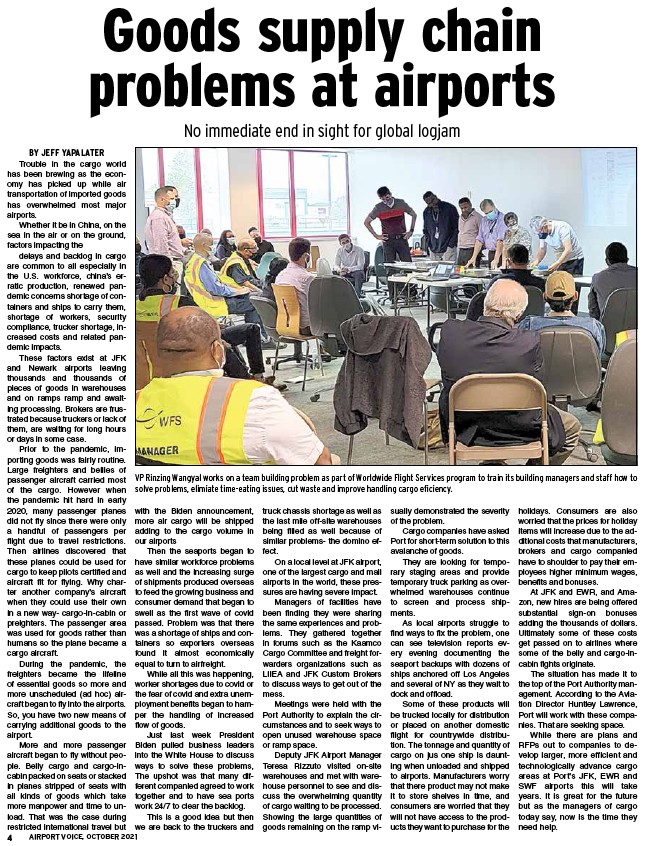
Goods supply chain
problems at airports
VP Rinzing Wangyal works on a team building problem as part of Worldwide Flight Services program to train its building managers and staff how to
solve problems, elimiate time-eating issues, cut waste and improve handling cargo eficiency.
4 AIRPORT VOICE, OCTOBER 2021
No immediate end in sight for global logjam
BY JEFF YAPALATER
Trouble in the cargo world
has been brewing as the economy
has picked up while air
transportation of imported goods
has overwhelmed most major
airports.
Whether it be in China, on the
sea in the air or on the ground,
factors impacting the
delays and backlog in cargo
are common to all especially in
the U.S. workforce, china’s erratic
production, renewed pandemic
concerns shortage of containers
and ships to carry them,
shortage of workers, security
compliance, trucker shortage, increased
costs and related pandemic
impacts.
These factors exist at JFK
and Newark airports leaving
thousands and thousands of
pieces of goods in warehouses
and on ramps ramp and awaiting
processing. Brokers are frustrated
because truckers or lack of
them, are waiting for long hours
or days in some case.
Prior to the pandemic, importing
goods was fairly routine.
Large freighters and bellies of
passenger aircraft carried most
of the cargo. However when
the pandemic hit hard in early
2020, many passenger planes
did not fly since there were only
a handful of passengers per
flight due to travel restrictions.
Then airlines discovered that
these planes could be used for
cargo to keep pilots certified and
aircraft fit for flying. Why charter
another company’s aircraft
when they could use their own
in a new way- cargo-in-cabin or
preighters. The passenger area
was used for goods rather than
humans so the plane became a
cargo aircraft.
During the pandemic, the
freighters became the lifeline
of essential goods so more and
more unscheduled (ad hoc) aircraft
began to fly into the airports.
So, you have two new means of
carrying additional goods to the
airport.
More and more passenger
aircraft began to fly without people.
Belly cargo and cargo-incabin
packed on seats or stacked
in planes stripped of seats with
all kinds of goods which take
more manpower and time to unload.
That was the case during
restricted international travel but
with the Biden announcement,
more air cargo will be shipped
adding to the cargo volume in
our airports
Then the seaports began to
have similar workforce problems
as well and the increasing surge
of shipments produced overseas
to feed the growing business and
consumer demand that began to
swell as the first wave of covid
passed. Problem was that there
was a shortage of ships and containers
so exporters overseas
found it almost economically
equal to turn to airfreight.
While all this was happening,
worker shortages due to covid or
the fear of covid and extra unemployment
benefits began to hamper
the handling of increased
flow of goods.
Just last week President
Biden pulled business leaders
into the White House to discuss
ways to solve these problems,
The upshot was that many different
companied agreed to work
together and to have sea ports
work 24/7 to clear the backlog.
This is a good idea but then
we are back to the truckers and
truck chassis shortage as well as
the last mile off-site warehouses
being filled as well because of
similar problems- the domino effect.
On a local level at JFK airport,
one of the largest cargo and mail
airports in the world, these pressures
are having severe impact.
Managers of facilities have
been finding they were sharing
the same experiences and problems.
They gathered together
in forums such as the Kaamco
Cargo Committee and freight forwarders
organizations such as
LIIEA and JFK Custom Brokers
to discuss ways to get out of the
mess.
Meetings were held with the
Port Authority to explain the circumstances
and to seek ways to
open unused warehouse space
or ramp space.
Deputy JFK Airport Manager
Teresa Rizzuto visited on-site
warehouses and met with warehouse
personnel to see and discuss
the overwhelming quantity
of cargo waiting to be processed.
Showing the large quantities of
goods remaining on the ramp visually
demonstrated the severity
of the problem.
Cargo companies have asked
Port for short-term solution to this
avalanche of goods.
They are looking for temporary
staging areas and provide
temporary truck parking as overwhelmed
warehouses continue
to screen and process shipments.
As local airports struggle to
find ways to fix the problem, one
can see television reports every
evening documenting the
seaport backups with dozens of
ships anchored off Los Angeles
and several of NY as they wait to
dock and offload.
Some of these products will
be trucked locally for distribution
or placed on another domestic
flight for countrywide distribution.
The tonnage and quantity of
cargo on jus one ship is daunting
when unloaded and shipped
to airports. Manufacturers worry
that there product may not make
it to store shelves in time, and
consumers are worried that they
will not have access to the products
they want to purchase for the
holidays. Consumers are also
worried that the prices for holiday
items will increase due to the additional
costs that manufacturers,
brokers and cargo companied
have to shoulder to pay their employees
higher minimum wages,
benefits and bonuses.
At JFK and EWR, and Amazon,
new hires are being offered
substantial sign-on bonuses
adding the thousands of dollars.
Ultimately some of these costs
get passed on to airlines where
some of the belly and cargo-incabin
fights originate.
The situation has made it to
the top of the Port Authority management.
According to the Aviation
Director Huntley Lawrence,
Port will work with these companies.
That are seeking space.
While there are plans and
RFPs out to companies to develop
larger, more efficient and
technologically advance cargo
areas at Port’s JFK, EWR and
SWF airports this will take
years. It is great for the future
but as the managers of cargo
today say, now is the time they
need help.