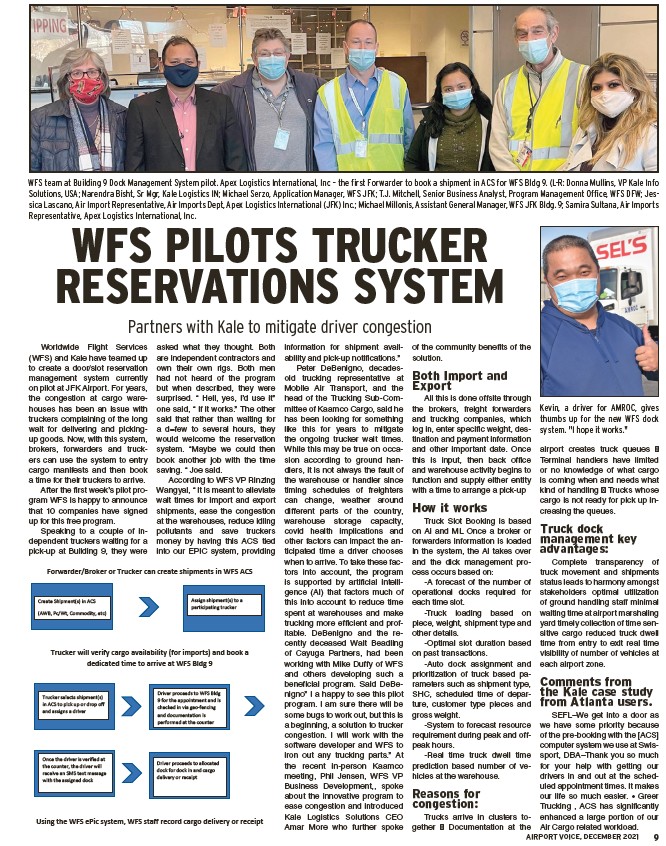
WFS team at Building 9 Dock Management System pilot. Apex Logistics International, Inc – the first Forwarder to book a shipment in ACS for WFS Bldg 9. (L-R: Donna Mullins, VP Kale Info
Solutions, USA; Narendra Bisht, Sr Mgr, Kale Logistics IN; Michael Serzo, Application Manager, WFS JFK; T.J. Mitchell, Senior Business Analyst, Program Management Office, WFS DFW; Jessica
Lascano, Air Import Representative, Air Imports Dept, Apex Logistics International (JFK) Inc.; Michael Millonis, Assistant General Manager, WFS JFK Bldg. 9; Samira Sultana, Air Imports
AIRPORT VOICE, DECEMBER 2021 9
Representative, Apex Logistics International, Inc.
WFS PILOTS TRUCKER
RESERVATIONS SYSTEM
Partners with Kale to mitigate driver congestion
Worldwide Flight Services
(WFS) and Kale have teamed up
to create a door/slot reservation
management system currently
on pilot at JFK Airport. For years,
the congestion at cargo warehouses
has been an issue with
truckers complaining of the long
wait for delivering and pickingup
goods. Now, with this system,
brokers, forwarders and truckers
can use the system to entry
cargo manifests and then book
a time for their truckers to arrive.
After the first week’s pilot program
WFS is happy to announce
that 10 companies have signed
up for this free program.
Speaking to a couple of independent
truckers waiting for a
pick-up at Building 9, they were
asked what they thought. Both
are independent contractors and
own their own rigs. Both men
had not heard of the program
but when described, they were
surprised. “ Hell, yes, I’d use it”
one said, “ If it works.” The other
said that rather than waiting for
a d=few to several hours, they
would welcome the reservation
system. “Maybe we could then
book another job with the time
saving. “ Joe said.
According to WFS VP Rinzing
Wangyal, “ It is meant to alleviate
wait times for import and export
shipments, ease the congestion
at the warehouses, reduce idling
pollutants and save truckers
money by having this ACS tied
into our EPIC system, providing
information for shipment availability
and pick-up notifications.”
Peter DeBenigno, decadesold
trucking representative at
Mobile Air Transport, and the
head of the Trucking Sub-Committee
of Kaamco Cargo, said he
has been looking for something
like this for years to mitigate
the ongoing trucker wait times.
While this may be true on occasion
according to ground handlers,
it is not always the fault of
the warehouse or handler since
timing schedules of freighters
can change, weather around
different parts of the country,
warehouse storage capacity,
covid health implications and
other factors can impact the anticipated
time a driver chooses
when to arrive. To take these factors
into account, the program
is supported by artificial intelligence
(AI) that factors much of
this into account to reduce time
spent at warehouses and make
trucking more efficient and profitable.
DeBenigno and the recently
deceased Walt Beadling
of Cayuga Partners, had been
working with Mike Duffy of WFS
and others developing such a
beneficial program. Said DeBenigno”
I a happy to see this pilot
program. I am sure there will be
some bugs to work out, but this is
a beginning, a solution to trucker
congestion. I will work with the
software developer and WFS to
iron out any trucking parts.” At
the recent in-person Kaamco
meeting, Phil Jensen, WFS VP
Business Development,, spoke
about the innovative program to
ease congestion and introduced
Kale Logistics Solutions CEO
Amar More who further spoke
of the community benefits of the
solution.
Both Import and
Export
All this is done offsite through
the brokers, freight forwarders
and trucking companies, which
log in, enter specific weight, destination
and payment information
and other important date. Once
this is input, then back office
and warehouse activity begins to
function and supply either entity
with a time to arrange a pick-up
How it works
Truck Slot Booking is based
on Ai and ML Once a broker or
forwarders information is loaded
in the system, the AI takes over
and the dick management process
occurs based on:
-A forecast of the number of
operational docks required for
each time slot.
-Truck loading based on
piece, weight, shipment type and
other details.
-Optimal slot duration based
on past transactions.
-Auto dock assignment and
prioritization of truck based parameters
such as shipment type,
SHC, scheduled time of departure,
customer type pieces and
gross weight.
-System to forecast resource
requirement during peak and offpeak
hours.
-Real time truck dwell time
prediction based number of vehicles
at the warehouse.
Reasons for
congestion:
Trucks arrive in clusters together
▪ Documentation at the
airport creates truck queues ▪
Terminal handlers have limited
or no knowledge of what cargo
is coming when and needs what
kind of handling ▪ Trucks whose
cargo is not ready for pick up increasing
the queues.
Truck dock
management key
advantages:
Complete transparency of
truck movement and shipments
status leads to harmony amongst
stakeholders optimal utilization
of ground handling staff minimal
waiting time at airport marshaling
yard timely collection of time sensitive
cargo reduced truck dwell
time from entry to exit real time
visibility of number of vehicles at
each airport zone.
Comments from
the Kale case study
from Atlanta users.
SEFL–We get into a door as
we have some priority because
of the pre-booking with the ACS
computer system we use at Swissport,
DBA–Thank you so much
for your help with getting our
drivers in and out at the scheduled
appointment times. It makes
our life so much easier. • Greer
Trucking , ACS has significantly
enhanced a large portion of our
Air Cargo related workload.
Forwarder/Broker or Trucker can create shipments in WFS ACS
Create Shipment(s) in ACS
(AWB, Pc/Wt, Commodity, etc)
Assign shipment(s) to a
participating trucker
Trucker will verify cargo availability (for imports) and book a
dedicated time to arrive at WFS Bldg 9
Trucker selects shipment(s)
in ACS to pick up or drop off
and assigns a driver
Driver proceeds to WFS Bldg
9 for the appointment and is
checked in via geo-fencing
and documentation is
performed at the counter
Once the driver is verified at
the counter, the driver will
receive an SMS text message
with the assigned dock
Driver proceeds to allocated
dock for dock in and cargo
delivery or receipt
Using the WFS ePic system, WFS staff record cargo delivery or receipt
Kevin, a driver for AMROC, gives
thumbs up for the new WFS dock
system. "I hope it works."